Vorbereitet für den Fall der Fälle
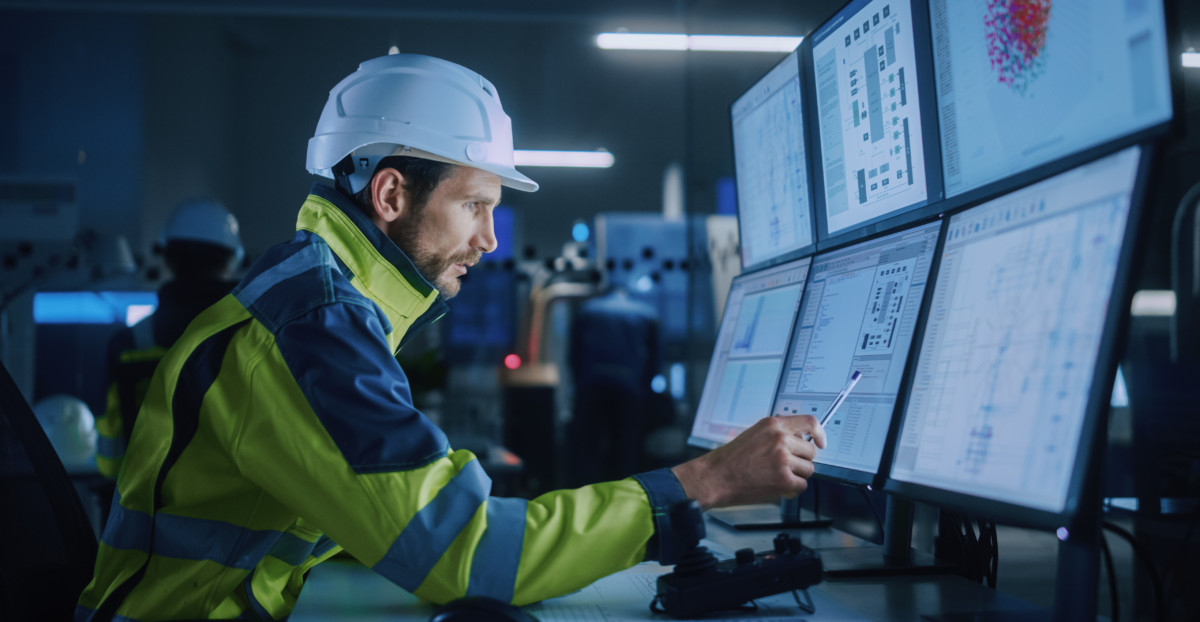
Eine Störung tritt meist während der Produktionszeiten auf und dann muss rasch reagiert werden. © Gorodenkoff/stock.adobe.com
Gefahren minimieren beim Beseitigen von Störungen an Maschinen und Anlagen: Tipps von der Berufsgenossenschaft Holz und Metall
Zeitdruck, fehlende Kommunikation oder unzureichende Hilfs- und Arbeitsmittel können bei einer Störungsbeseitigung an Maschinen und Anlagen zu gefährlichen Situationen führen und schwere Unfälle zur Folge haben. Eine Störung – und damit ein ungeplanter Anlagenstillstand – tritt meist während der Produktionszeiten auf und dann muss rasch reagiert werden. „Gedanklich vorab durchgespielte Störungsszenarien, eingeübte Prozesse und Vorgehensweisen sowie eine präventive Instandhaltung ermöglichen es hier im Zusammenspiel, Unfallrisiken zu reduzieren“, sagt Andreas Köster, Fachreferent für die Instandhaltung von Maschinen und Anlagen bei der Berufsgenossenschaft Holz und Metall (BGHM).
Das vermeintlich Unplanbare bestmöglich planen
Es sind meist Wechselwirkungen zwischen Maschine, Mensch und Umgebung, die zu Störungen führen. „Einflussfaktoren sind beispielsweise Verschleiß, eine Fehlbedienung oder Umgebungsfeuchtigkeit“, erläutert Köster. Die Suche nach der Störungsursache und deren Beseitigung kann sich somit von Fall zu Fall unterschiedlich komplex gestalten. Technischen, organisatorischen und personellen Herausforderungen lässt sich hier mit vorausschauenden Analysen und Gefährdungsbeurteilungen begegnen. Dazu gehört auch, Meldeketten zu definieren und eindeutige Verantwortlichkeiten festzulegen.
Um im Störungsfall effizient und gefahrenminimiert agieren zu können, ist etwa das Lockout-Tagout-Prinzip als Arbeitsschutzverfahren bewährt: Die Maschine wird abgeschaltet, gegen Wiedereinschalten gesichert, und die Restenergien werden abgebaut. In der sogenannten 4-Rang-Methode entspricht dies Rang 1 und damit der ersten von vier Schutzstufen, um Gefahren durch laufende Maschinen und Anlagen zu minimieren. Bei einem – mit den einzelnen Rangstufen – steigenden Unfallrisiko werden die Sicherheitsmaßnahmen und Vorgehensweisen den Möglichkeiten vor Ort entsprechend angepasst. Dabei gilt es, das Risikominimierungsprinzip einzuhalten. Zeitdruck und Stress können durch ein eingespieltes Team, bereitgelegte Arbeitsmittel und vorhandene Ersatzteile reduziert werden. Klare betriebliche Anweisungen, zum Beispiel wer unter welchen Voraussetzungen welche Störungen beheben darf, sorgen für Gewissheit bei den Abläufen. Allgemein gilt: Je komplexer die Störungsbeseitigung, desto höher die personellen Anforderungen hinsichtlich Qualifikation und Befähigung.
Maschinen klassifizieren und in Stand halten
Entscheidend bei Störungsszenarien ist folglich der Blick auf die verwendeten Energiearten und potenzielle Restenergien als größte Gefahrenquelle: Für jede Maschine im Betrieb sollten diese Energieformen klar identifiziert sein. Bei der Priorisierung von Instandhaltungsmaßnahmen hilft die so genannte ABC-Analyse. Dabei werden die Maschinen gemäß ihrer Bedeutung für den Produktionsprozess und der Ausfallfolgen klassifiziert. Nicht zuletzt gilt: Mit regelmäßigen Wartungen lassen sich Störungen reduzieren – mitunter die effektivste Vorsorge vor Gefährdungen.