- Editorial
- Schwerpunkt
- Zahlen & Fakten
- Sicher und gesund arbeiten
- Gut führen
- Nachhaltig und innovativ arbeiten
- Alles, was Recht ist
- Produkte & Märkte
- Damals
- Ausblick
Schrauben für die Zukunft
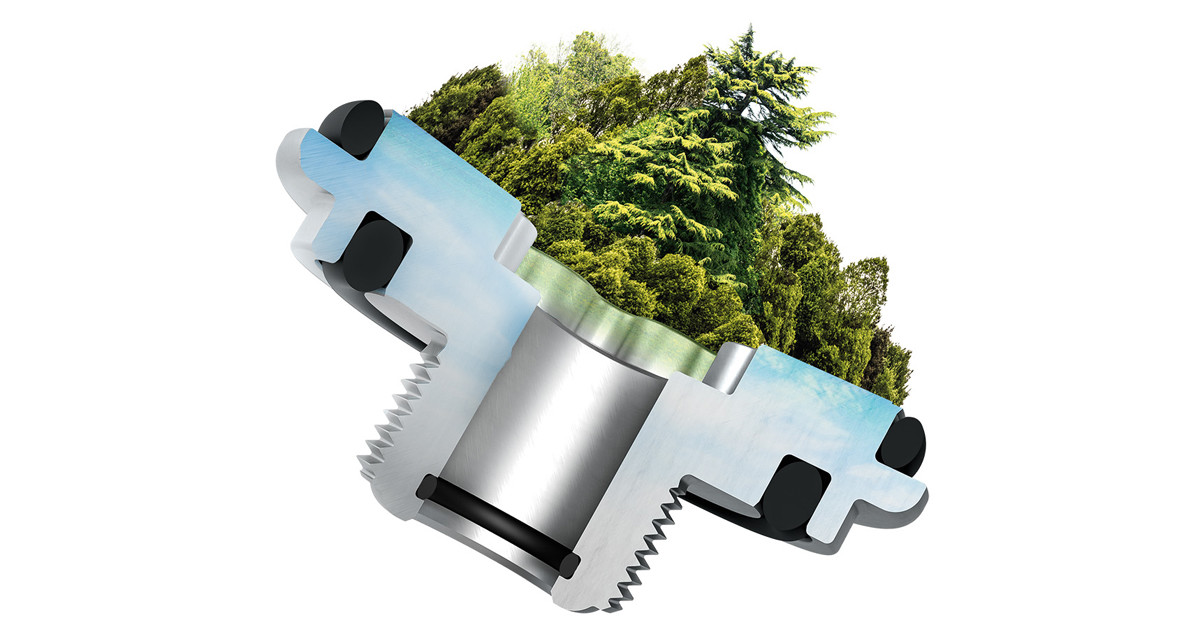
Für die Schrauben der „Conform Next“-Reihe benötigt Arnold fast ein Drittel weniger Material. Insgesamt werden die CO2-Emissionen bei der Produktion um 45 Prozent reduziert. Foto: Arnold Umformtechnik
Kann eine Schraube die Welt retten? Wohl kaum. Aber sie kann einen kleinen Teil dazu beitragen. Erst recht, wenn die Produktion in ein Konzept zur Nachhaltigkeit, Ressourcen- und Energieeffizienz eingebettet ist. Davon ist die Arnold Umformtechnik GmbH & Co. KG überzeugt.
Um alle spannenden Reportagen zur Arbeitssicherheit, Gesundheitsprävention und nachhaltigem Arbeiten unbeschränkt lesen zu können, registrieren Sie jetzt für einen Gratismonat – läuft automatisch aus!