- Editorial
- Schwerpunkt
- Sicher und gesund arbeiten
- Gut führen
- Nachhaltig und innovativ arbeiten
- Alles, was Recht ist
- Praxis
- Produkte & Märkte
- Damals
- Ausblick
Hat Lithium bald ausgedient?
Die Entwicklung der modernen Batterie
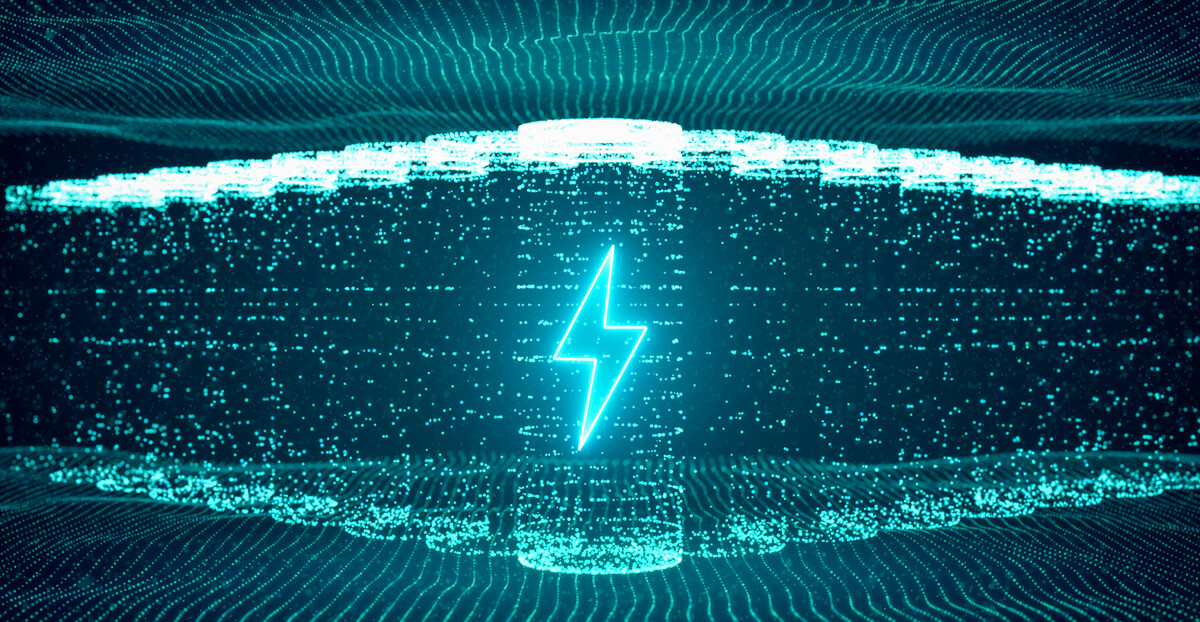
Illustration: Adobe Stock / ZETHA WORK
Akkus auf Basis von Lithium-Ionen sind das Nonplusultra, wenn es um Energiespeicherung geht. Die Nachhaltigkeit der Batterien muss allerdings noch verbessert werden. Deshalb werden derzeit Alternativen entwickelt, bei denen in puncto Leistungsfähigkeit und Sicherheit keine Abstriche gemacht werden müssen.
Um alle spannenden Reportagen zur Arbeitssicherheit, Gesundheitsprävention und nachhaltigem Arbeiten unbeschränkt lesen zu können, registrieren Sie jetzt für einen Gratismonat – läuft automatisch aus!