- Titelthema
- Editorial
- Schwerpunkt
- Zahlen & Fakten
- Sicher und gesund arbeiten
- Gut führen
- Nachhaltig und innovativ arbeiten
- Alles, was Recht ist
- Produkte & Märkte
- Damals
- Ausblick
Raus aus dem Käfig!
Die Zukunft der Mensch-Roboter-Kollaboration
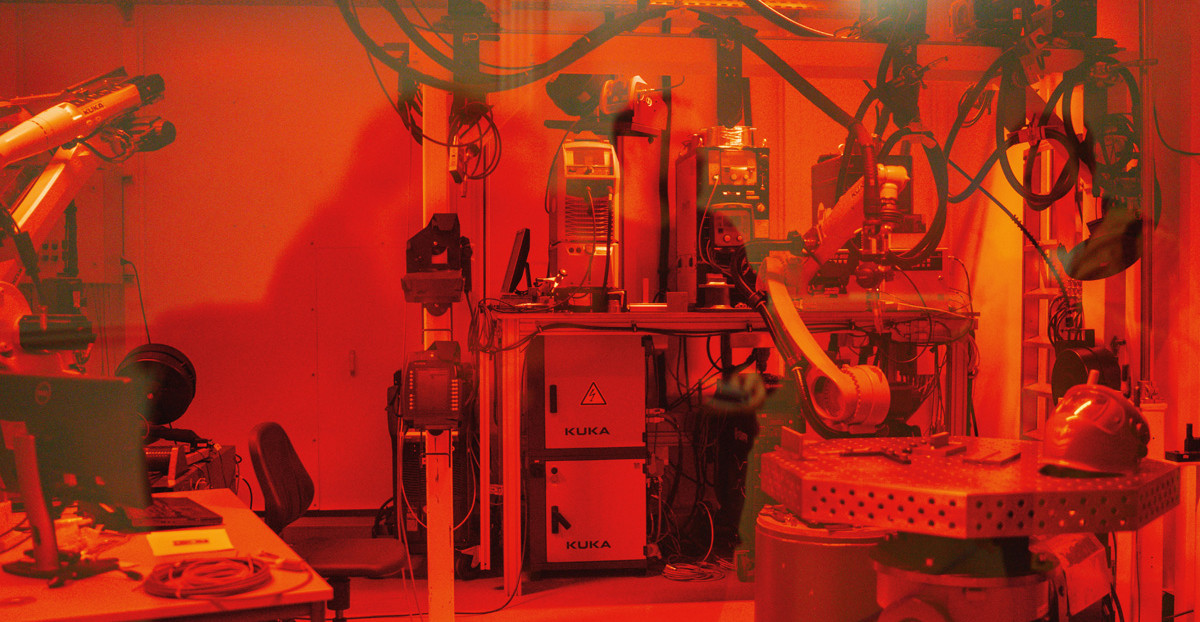
Achtung, Roboter bei der Arbeit! Die klassischen Industrieroboter müssen hinter Schutzwänden ihrer Tätigkeit nachgehen, um keine Menschen zu gefährden. Inzwischen wird der Betrieb kollaborierender Roboter aber mehr und mehr zur Selbstverständlichkeit. Foto: Iris Wagner-Hoppe/photoresque
Wenn Mensch und Roboter zusammenarbeiten sollen, müssen die Maschinen gewisse Anforderungen erfüllen. In erster Linie an die Sicherheit. Aber sie müssen auch einfach bedienbar und flexibel einsetzbar sein. Daran arbeitet der Augsburger Roboterhersteller Kuka.
Um alle spannenden Reportagen zur Arbeitssicherheit, Gesundheitsprävention und nachhaltigem Arbeiten unbeschränkt lesen zu können, registrieren Sie jetzt für einen Gratismonat – läuft automatisch aus!