- Editorial
- Schwerpunkt
- Sicher und gesund arbeiten
- Gut führen
- Nachhaltig und innovativ arbeiten
- Alles, was Recht ist
- Produkte & Märkte
- Damals
- Ausblick
Unfallschwerpunkt Maschine entschärfen
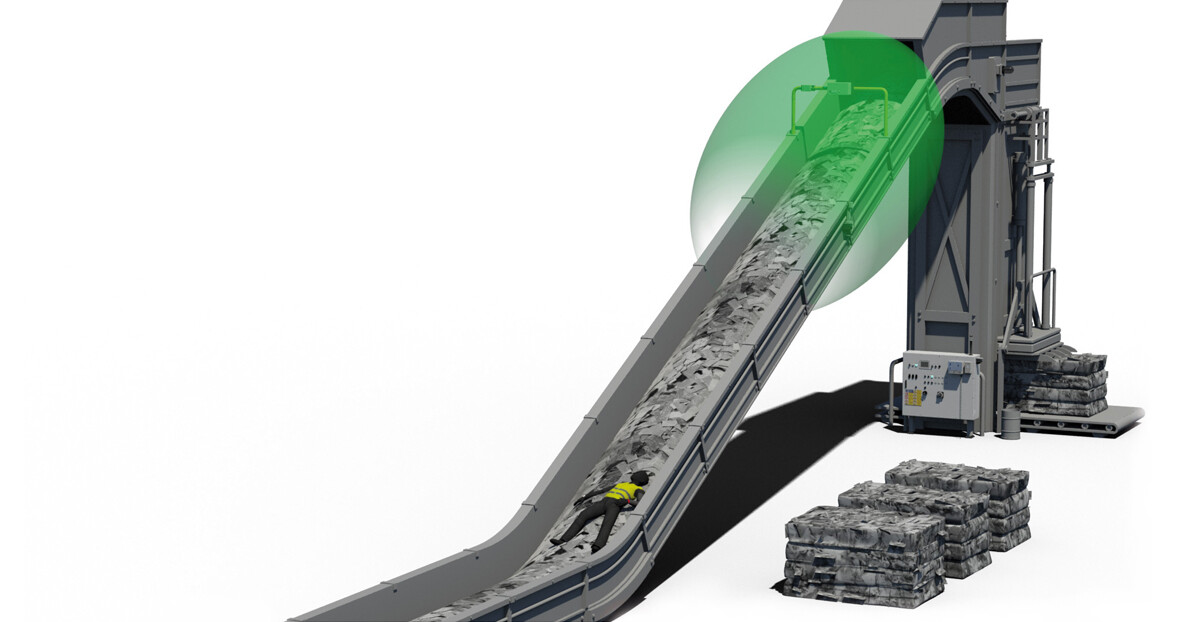
U-Tech Press: Das Personenschutzsystem erkennt mittels Funk-Technologie, wenn sich eine Person dem Gefahrenbereich nähert. Dann schaltet es das Förderband automatisch ab. Grafik: U-Tech
Maschinen bilden einen Schwerpunkt für Unfälle im industriellen Arbeitsalltag. Doch oft führt erst menschliches Fehlverhalten zu Ereignissen mit Personenschäden. Arbeitgeber sind aufgerufen, Maßnahmen in die Wege zu leiten, um maximalen Schutz zu gewährleisten.
Um alle spannenden Reportagen zur Arbeitssicherheit, Gesundheitsprävention und nachhaltigem Arbeiten unbeschränkt lesen zu können, registrieren Sie jetzt für einen Gratismonat – läuft automatisch aus!